Our Reconditioning Process
Our reconditioned Aga cookers undertake a meticulous reconditioning process that involves thorough inspection, repair, and refurbishment to bring them back to showroom condition.
Our team of skilled technicians assess each compartment of the cooker, replacing parts with new, ensuring that all our reconditioned cookers meet our high-quality standards
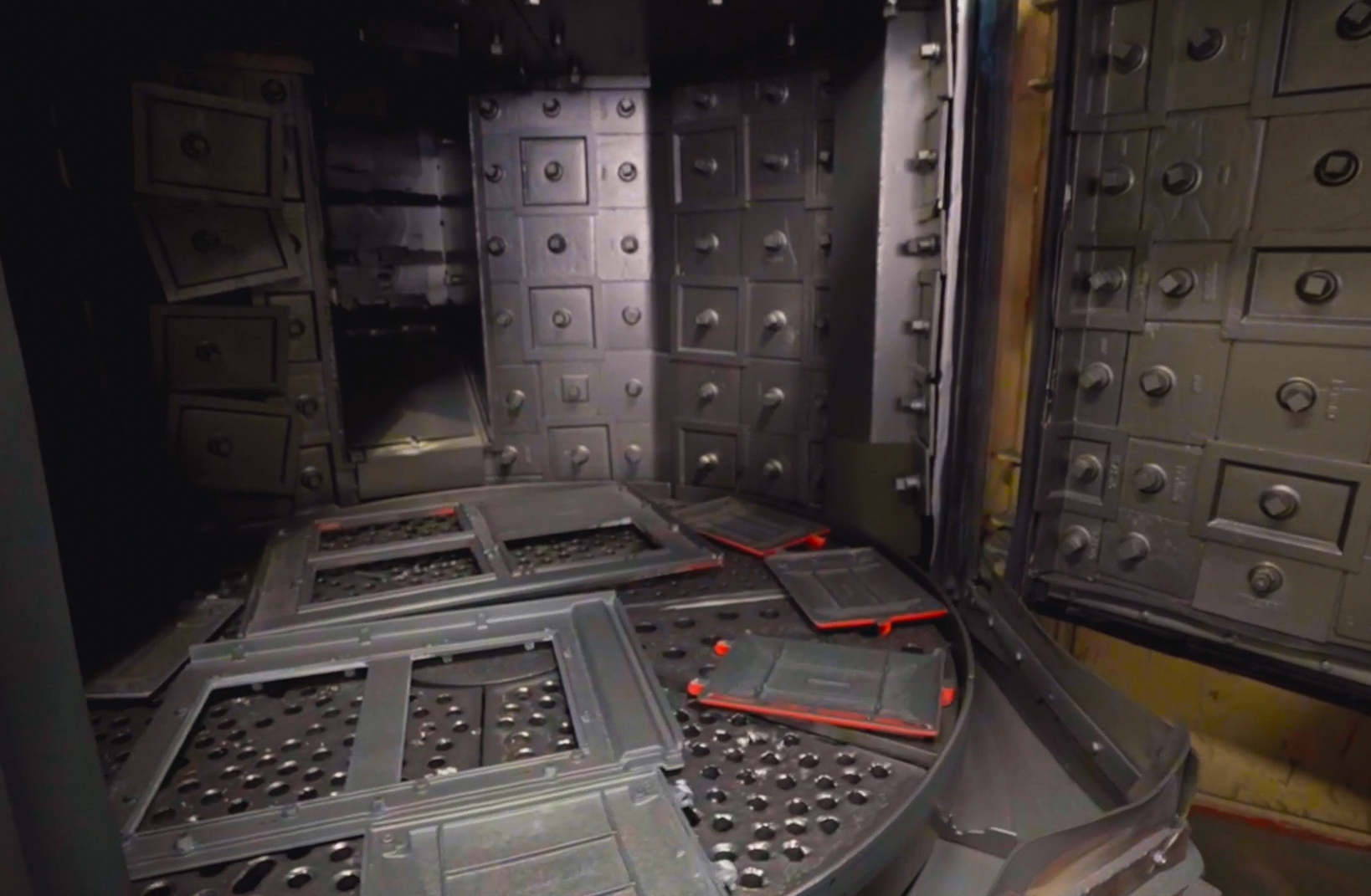
Returning the Cast-Iron back to its Original Form
Firstly, the outer fascia of each cooker is carefully removed and the enamel is lifted off through a process called shotblasting.
Shotblasting involves propelling abrasive materials at high speeds to clean and prepare the surface of the cast-iron components.
This removes layers of old enamel, effectively returning the cast-iron back to its original form.
Our skilled technicians meticulously inspect each component to ensure they meet our high standards before proceeding to the next stage of the reconditioning process.
Deep Gloss Vitreous Enamel Coating
All of our reconditioned Aga cookers are finished with deep gloss, hardwearing, vitreous enamel.
The vitreous enamel used on Aga cookers is in fact, a type of coloured glass which is a compound of natural minerals including glass particles and metal oxides. These materials are milled to a fine powder and mixed to create a “frit”.
The enamel is then applied to the cast iron in several layers, undergoing three separate firings at up to 800 degrees Celsius to achieve the high gloss finish that Aga cookers are famed for.
Vitreous enamel is long-lasting, durable and easy to clean. Each batch of enamel is hand-mixed and finished. This gives each cooker it’s unique character and makes it individual to you.
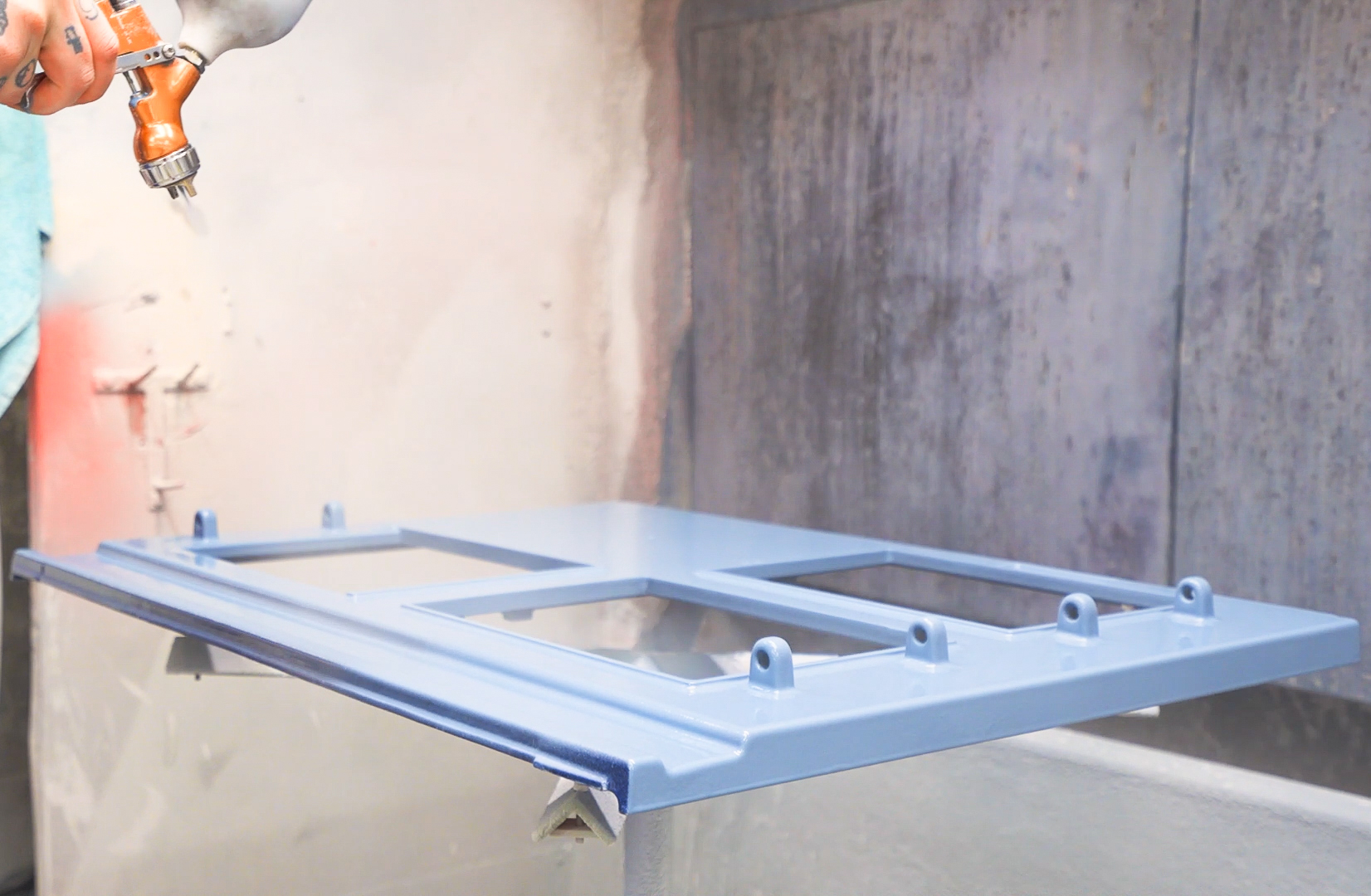
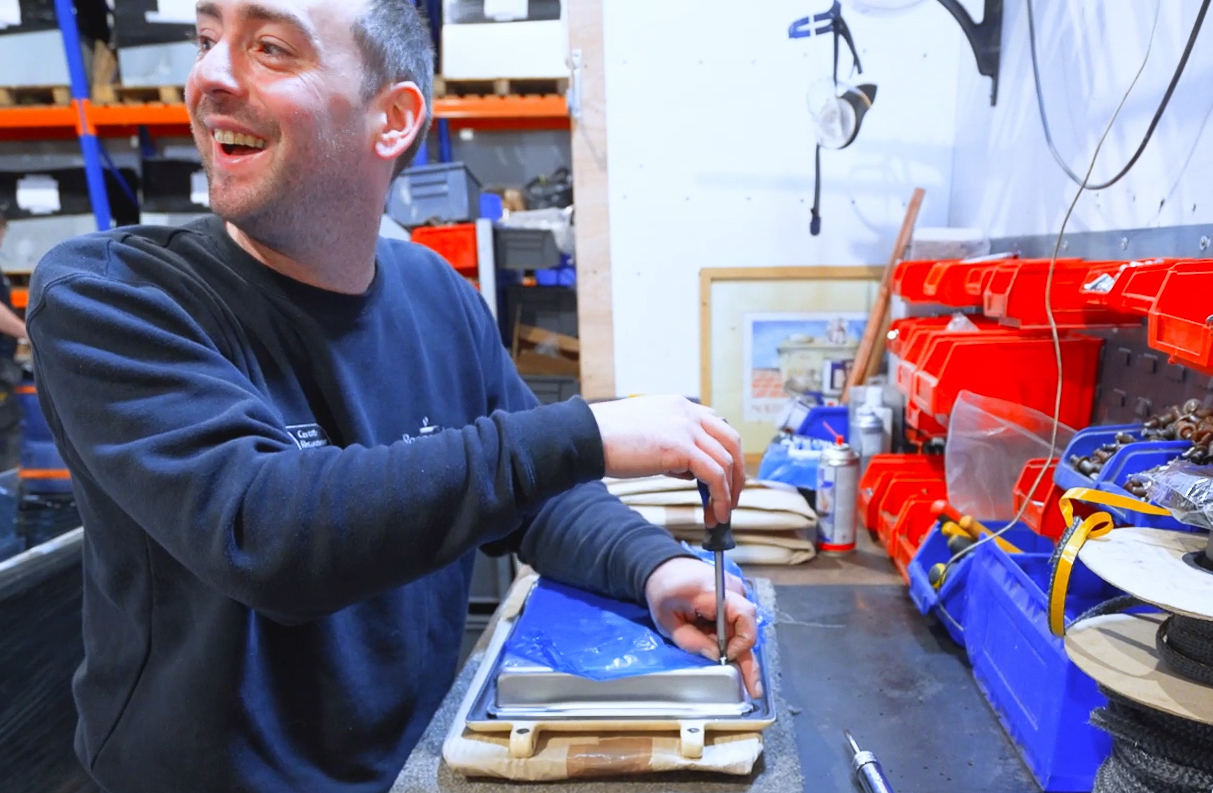
Hand Finished by Our In-house Technicians
Once the enamelling process is completed, our team at the workshop individually hand-finish each Aga cooker.
This final stage of the restoration process involves assembling all the components, adjusting any moving parts, and conducting rigorous quality checks to ensure everything is in perfect working order. Our technicians take pride in their craftsmanship, paying attention to every detail to ensure that each Aga cooker meets our exacting standards.
From replacing door liners and rope seals, to adding brand new lids and chrome hardware, our skilled engineers pay particular attention to all the finer details.
Delivery Right into Your Home
Once the cooker has been fully reconditioned, it is carefully packaged up ready for delivery by our own friendly team who hand deliver all across the UK.
The delivery date is confirmed when your order is placed. The day before delivery our team will let you know their estimated time of arrival.
Once they arrive with the you, they will carefully navigate the cooker through your property using specialist moving equipment. Our team are professionals and will take great care of your property at all times.
Our team will install the cooker and even show you how it works!
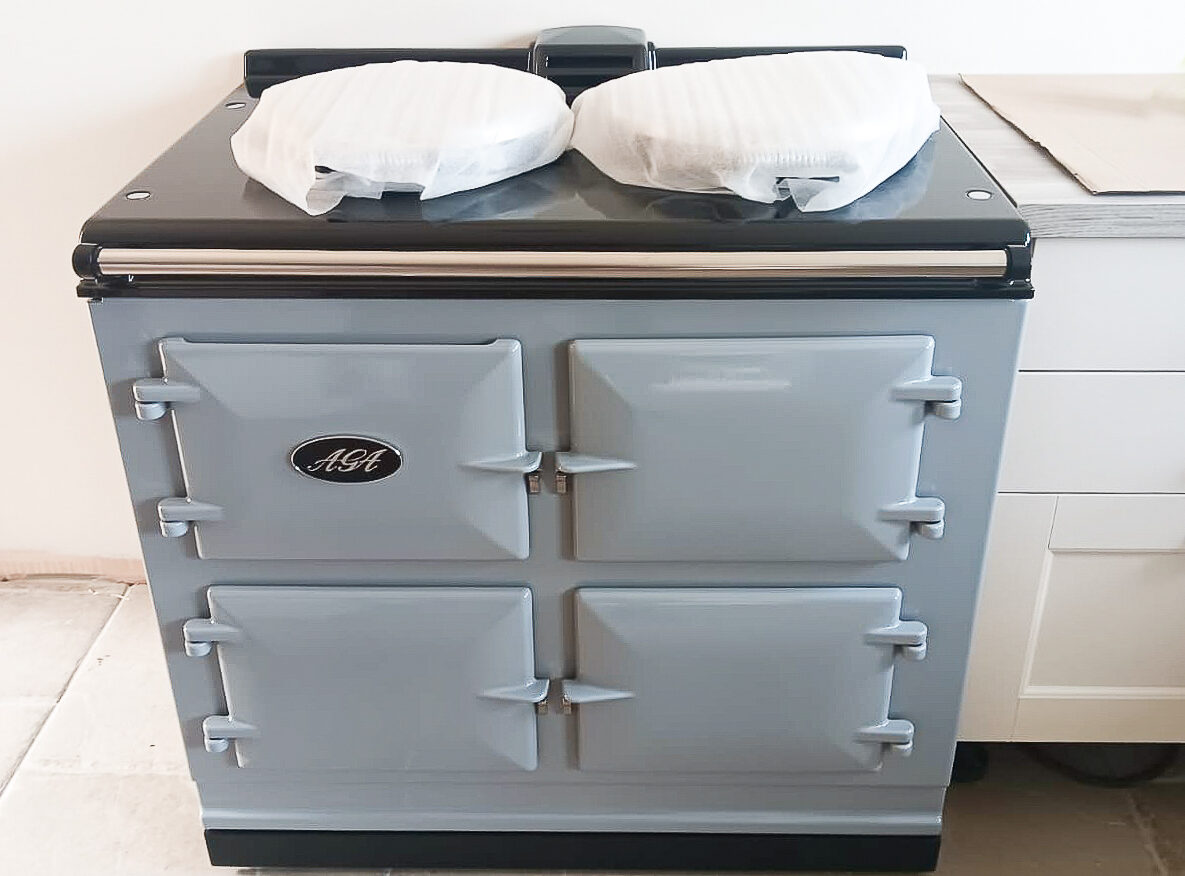
We are proud to ensure that every cooker that we recondition is to the highest level of quality
Conversation Starter
Our team are here to help. Please contact 01625 569 445 to speak to our team directly.